Luted Crucible Bronze Casting
31 July 2014
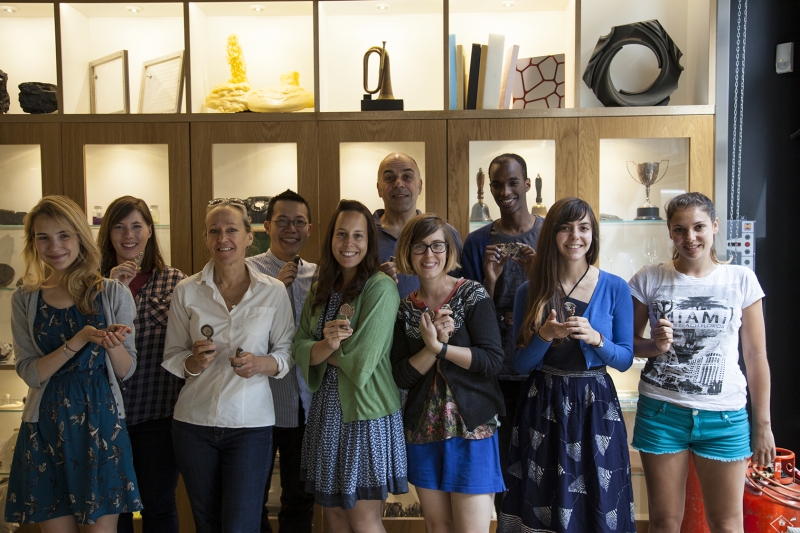
Last week we were shown the delights of hot metal by artist Piers Watson, who taught us an ancient bronze casting technique called "Luted Crucible Bronze Casting”.
'Luted' or sealed crucible casting is a low-cost and low-tech method of casting, relatively unknown outside India and West Africa. It involves sealing the raw ingredients for bronze - copper and tin - into one half of a peanut-shaped crucible made from mud. The other half contains the wax model to be cast. The whole thing is baked in a furnace, and when the metal is molten it is flipped over, and the liquid bronze fills the cavity left by the wax.
Piers has been teaching this method all over the world and it was a treat to have him here for the whole week, leading a fantastic step-by-step exploration of how bronze making has been done since the early days of its history.
During the week we explored the fundamental techniques, making our own wax object, and covering it in numerous layers of different mixes of sand, clay and rice husks, and sealing in the copper and tin. Finally, we cast the crucibles in Piers' home-made gas furnace. Once cracked open they revealed the magical objects inside.
Day 1: Using 10g of bees wax we made our objects, bearing in mind the technique may not work with complex forms. Once we had made our objects which ranged from a detailed brain, animal figures and a hammer and sickle to more experimental objects with embedded mica, it was time to add the first layer of clay. It incorporated very fine sand to catch all the detail of the wax models.
Day 2: Today’s layer involved a mix of coarse yellow and fine white clay with rice husks. After much mixing (the rice husks were pretty vicious on the hands!) and a dash of water we carefully layered the clay around our objects. In addition we had to form a funnel shape around the top of the object. This would enable the molten metal to flow into the cavity where the wax model had been. These extra layers of clay help to protect the inner detailed layer from the intense heat inside the furnace. We also made our crucible cups, where our metals would be contained. These were left to dry overnight.
Day 3: To make bronze you can use a few different 'recipes', some include arsenic or lead to modify the properties. For obvious safety reasons, we used plain copper and tin. We used 10 times the weight of the wax in copper, and we could choose to either use 10% or 20% of tin (20% would give make your object harder). Once measured and weighed with great accuracy, we joined the crucibles to the objects using another layer of the clay and rice husk mix. These were then left to dry overnight.
Day 4: This was a shorter day, where we built the finally clay layer over the entire object to ensure it was fully sealed and ready to be fired the following day. They were left to dry overnight for the final time.
Day 5: The big day, the moment of truth. Will our objects come out how we wanted them to? After an early start, Piers homemade furnace was roaring and the first objects were in. They didn't spend that long in the furnace, around 20 minutes, some took longer about 1hour max. Piers, master of the furnace, pulled them out and gave them a gentle shake to see if all the metals had melted - something you can only tell by experience. Once he was happy that they were all fully molten it was time to pull it out, tip it upside down which allowed for the metal to flow into where the wax once was (the wax burns away in the heat leaving an empty mould for the melts to flow into). After the crucible had cooled, we cracked it open to reveal our objects.
Much fun was had by all, there were some fantastic outcomes and we can't wait for Piers to come back again.
To see some more pictures visit our Facebook page or flickr.