Studio Visit to J & FJ Baker Tannery
12 August 2016
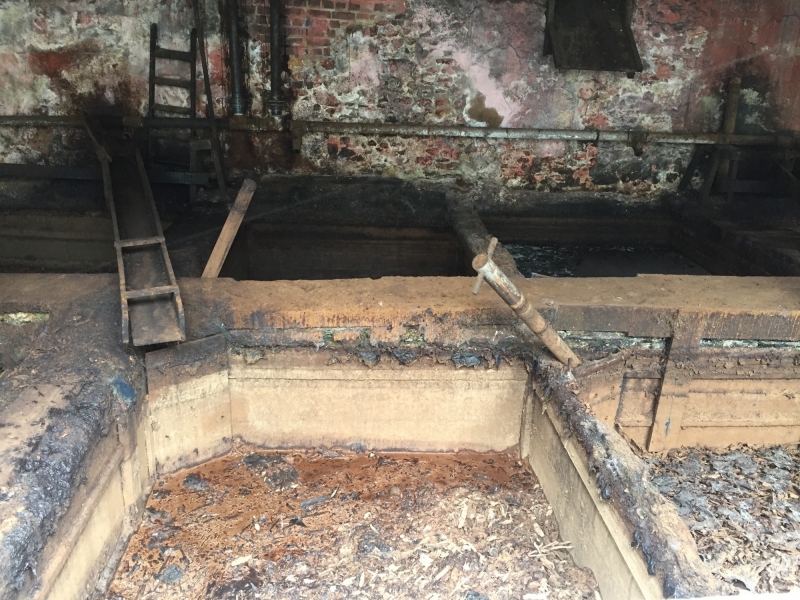
The second visit of my trip away, was to Britain’s last remaining oak bark tannery, J & FJ Baker & Co in Colyton. Upon arriving, I meandered through whitewashed buildings in search of Andrew Parr, who was going to show me around. There has been a tannery on the site since before records began. It was very common to have lots of tanneries, as hides would not be transported but tanned on site. The Parr family bought the tannery in 1862, and Andrew is the 5th generation at the helm.
Andrew appeared from a small office near the carpark and after quick introductions we set off strolling around the tannery, from the start of the process right to the end. We began the tour with the raw hides that come in on pallets, all salted to preserve the hides until required. The hides are hung and soaked in multiple lime baths of varying strengths for 3 weeks. The lime bath loosens the hair from the hide, allowing it to be easily removed in the teeth of the machine. The fat on the other side of the hide swells, which makes it easy to remove in the teeth of another machine. The fat is sent for cleaning and is repurposed and some is also repurposed on site, Andrew’s latest invention, a sustainable boiler, which he showed me later on our tour. Using a mixture of hair and fat, he creates a sausage, which is fed up a conveyor belt system into the boiler which fires to create heat for the winter months. The wastewater from the lime baths can also be put back into the river.
Their tanning process uses oak bark, which is abundant in Britain, whereas France and Italy use chestnut. The oak bark is stripped from the trees in spring and summer and then sent to the tannery where it sits for two to three years until it is fully dried. Once dried it is ground into small chunks using the water wheel and grinder. The bark is then soaked using cold water to extract the tanning liquor. This is a similar process to that of making a cup of tea, but using cold water. Once the liquor is strong enough, its pumped up into the tan yard into one of 72 pits. The tops pits are the stronger ones and each week the tan gets weaker but it is still slightly tannic and acidic. Each week the tannic solution moves down a pit as it weakens, and new hides begin in the weakest liquor and move progressively up to the higher strength.
You may notice that the hides are hung on battens; this is to allow the liquor to fully engulf the hide and creates an even colour and tannage. After three months hanging on the battens the hides are laid flat and placed in much deeper pits with the oak bark. Andrew described it as an ‘enormous sandwich of hide and oak’. The hides will rest here for nine months to complete the 12 month tanning process. At this point, the leather is finally removed, drained for two to three days and is then ready to be finished. The leather is hand stained using natural stains and oils, and then waxed using their own special blends.
As we finished our tour in the packing room, which has most brilliant set of huge scales, (random fact: leather is still sold in pounds) I noticed that there were some off-cuts. Andrew has very kindly donated some beautiful cuts of leather for our Materials Library. We have a piece of ‘full grain Australian Nut pull up’. ‘Full grain’ is the most expensive and highest grade of leather where the hides are used with the skin surface as is, showing the grain and marks accumulated by the animal. ‘Australian Nut’ refers to the colour of the leather and ‘pull up’ means that it is deeply impregnated with oils and waxes. When this type of leather is bent or pulled the oils move around within the skin causing lighter tones and interesting colors to become visible. He also donated a natural tan shoe sole, a piece of calf leather and a larger section of natural tan leather.
The slow tanning process creates leather which is lightweight, has a high tensile strength, is hard wearing, and has a beautiful open grain. It is ideal for shoes and saddlery. The leather is sold to some of the most exclusive places worldwide and is becoming highly sought after. Andrew Parr has 20 members of skilled staff, and they take over a year to produce what I would say is the most beautiful leather I have ever seen.
Thank you to Andrew for taking most of your afternoon showing me around the tannery. It was absolutely brilliant and I want to come back already, the smell didn’t put me off at all.
For more information about the tannery visit their website
To see more pictures visit Flickr or our Facebook page.